Implementamos soluções de automação que modernizam sua indústria, aumentando a eficiência, produtividade e inteligência operacional. Acelere sua transformação digital com tecnologias avançadas e inovação constante.

Automação Industrial
Conduzimos nas indústrias a implementação de soluções para transformação digital e modernização, tornando-as mais eficientes, produtivas e inteligentes através da tecnologia robótica, tecnologia de automação e tecnologias com plataformas de softwares.
Esses avanços não apenas aumentam a competitividade das empresas no mercado global, mas também promovem a sustentabilidade ao otimizar o uso de recursos e reduzir desperdícios. A integração de sistemas inteligentes permite a coleta e análise de dados em tempo real, facilitando a tomada de decisões estratégicas e proativas. Além disso, a automação de processos repetitivos libera os colaboradores para se concentrarem em tarefas de maior valor agregado, incentivando a inovação e a criatividade dentro da organização.
Ao investirmos em tecnologias emergentes como inteligência artificial, Internet das Coisas (IoT) e big data, estamos não apenas transformando a maneira como as indústrias operam, mas também preparando-as para os desafios do futuro. Nossa abordagem personalizada garante que cada solução seja adaptada às necessidades específicas de cada cliente, assegurando um retorno sobre o investimento significativo e duradouro.
Assim, continuamos a liderar o caminho rumo a um futuro mais conectado, eficiente e sustentável, onde a tecnologia e o talento humano caminham juntos para alcançar o sucesso.
Consultoria para a jornada da digitalização industrial
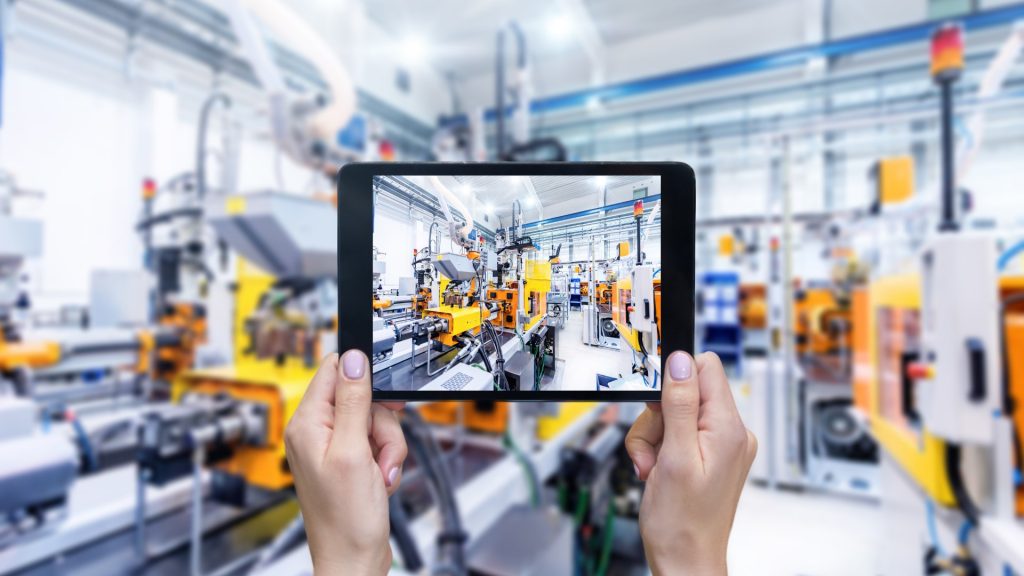
O que é consultoria para a jornada da digitalização industrial?
A consultoria para a jornada da digitalização industrial é um serviço especializado que auxilia empresas a implementarem tecnologias digitais em seus processos produtivos. Essa jornada envolve uma transformação profunda, desde a coleta e análise de dados até a automação de tarefas e a criação de produtos e serviços mais inteligentes.
A digitalização industrial, também conhecida como Indústria 4.0, oferece uma série de benefícios para as empresas:
- Aumento da eficiência: Automação de processos, otimização da produção e redução de desperdícios.
- Melhoria da qualidade: Controle de qualidade em tempo real e detecção precoce de falhas.
- Maior flexibilidade: Adaptação rápida a mudanças no mercado e personalização de produtos.
- Tomada de decisões mais precisas: Análise de dados em tempo real para otimizar a produção e a logística.
- Inovação: Desenvolvimento de novos produtos e serviços, além de modelos de negócios mais eficientes.
A consultoria para a jornada da digitalização industrial é um investimento estratégico para as empresas que desejam se manter competitivas no mercado atual. Ao contar com o apoio de especialistas, as empresas podem acelerar a transformação digital, otimizar seus processos e alcançar resultados superiores.
Uma consultoria especializada em digitalização industrial oferece diversas vantagens:
- Diagnóstico: Identificação das necessidades específicas de cada empresa e das oportunidades de melhoria.
- Elaboração de uma estratégia: Criação de um plano de ação personalizado para a implementação das tecnologias digitais.
- Implementação: Assistência técnica na implantação das soluções escolhidas, garantindo a integração com os sistemas existentes.
- Treinamento: Capacitação dos colaboradores para o uso das novas tecnologias e ferramentas
- Acompanhamento contínuo: Monitoramento dos resultados e ajustes na estratégia, conforme necessário.
- Agilidade: Aceleração do processo de digitalização, evitando erros e retrabalhos.
- Expertise: Acesso a conhecimentos e tecnologias de ponta, além de melhores práticas do mercado.
- Redução de riscos: Minimização dos riscos associados à implementação de novas tecnologias.
- Retorno sobre o investimento: Aumento da eficiência, da qualidade e da competitividade da empresa.
Plataforma de inteligência artificial para manufatura
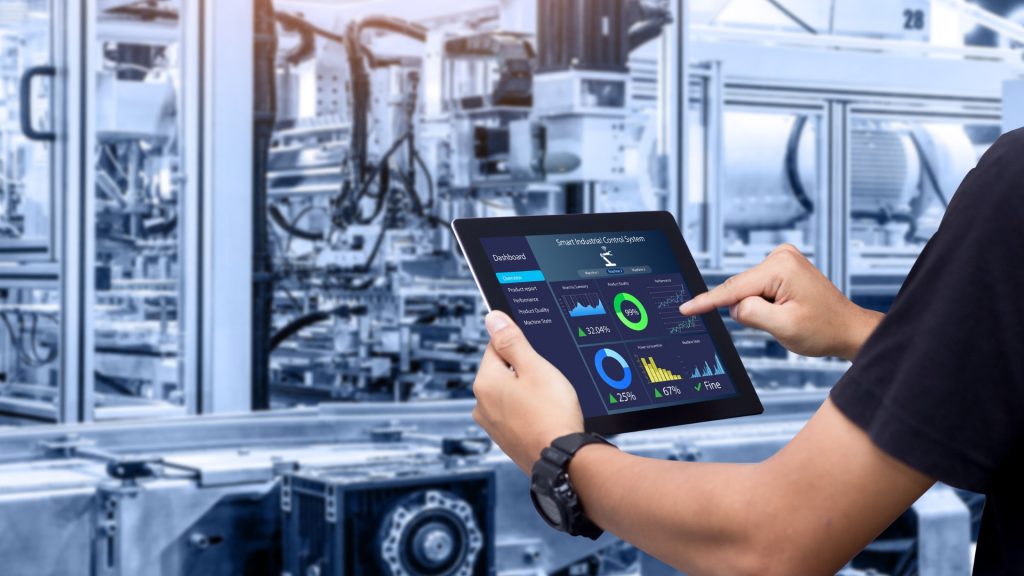
O que é uma plataforma de inteligência artificial para manufatura?
Imagine uma fábrica onde as máquinas se comunicam, preveem falhas e otimizam a produção de forma autônoma. Essa é a promessa das plataformas de Inteligência Artificial (IA) para a manufatura. Essas plataformas utilizam algoritmos avançados para analisar grandes volumes de dados gerados pelos processos industriais, proporcionando insights valiosos para a tomada de decisões e a otimização das operações.
Como funciona?
Essas plataformas integram diversos sensores, sistemas de controle e softwares de gestão, coletando dados em tempo real sobre o desempenho das máquinas, a qualidade dos produtos, o consumo de energia e outros indicadores-chave. A IA processa esses dados, identificando padrões, tendências e anomalias, e gerando alertas e recomendações para os operadores.
- Aumento da Produtividade: A otimização dos processos e a redução dos tempos de parada das máquinas resultam em um aumento significativo da produção.
- Melhoria da Qualidade: A detecção precoce de defeitos e a análise preditiva permitem garantir a qualidade dos produtos e reduzir os custos com retrabalho.
- Redução de Custos: A otimização do consumo de energia, a diminuição da manutenção não programada e a melhoria da gestão de estoque contribuem para a redução dos custos operacionais.
- Tomada de Decisões Mais Precisas: Os insights gerados pela IA permitem aos gestores tomar decisões mais estratégicas e baseadas em dados.
- Flexibilidade e Adaptabilidade: As plataformas de IA permitem que as indústrias se adaptem rapidamente às mudanças do mercado e às novas demandas dos clientes.
- Manutenção Preditiva: A IA pode prever falhas em equipamentos, permitindo realizar a manutenção de forma programada e evitando paradas inesperadas.
- Controle de Qualidade: Inspeção automática de produtos, detecção de defeitos e garantia da conformidade com os padrões de qualidade.
- Otimização da Cadeia de Suprimentos: Previsão da demanda, gestão de estoque, otimização da logística e redução de custos.
- Gestão da Energia: Monitoramento do consumo de energia, identificação de oportunidades de economia e otimização dos processos energéticos.
- Manufatura Aditiva: Otimização dos processos de impressão 3D, desenvolvimento de novos materiais e personalização de produtos.
Em resumo, as plataformas de Inteligência Artificial para Manufatura representam uma revolução na indústria, proporcionando maior eficiência, produtividade e competitividade. Ao transformar os dados em conhecimento, essas plataformas permitem que as empresas se adaptem às demandas do mercado e garantam a sua sustentabilidade a longo prazo.
Outras ofertas:
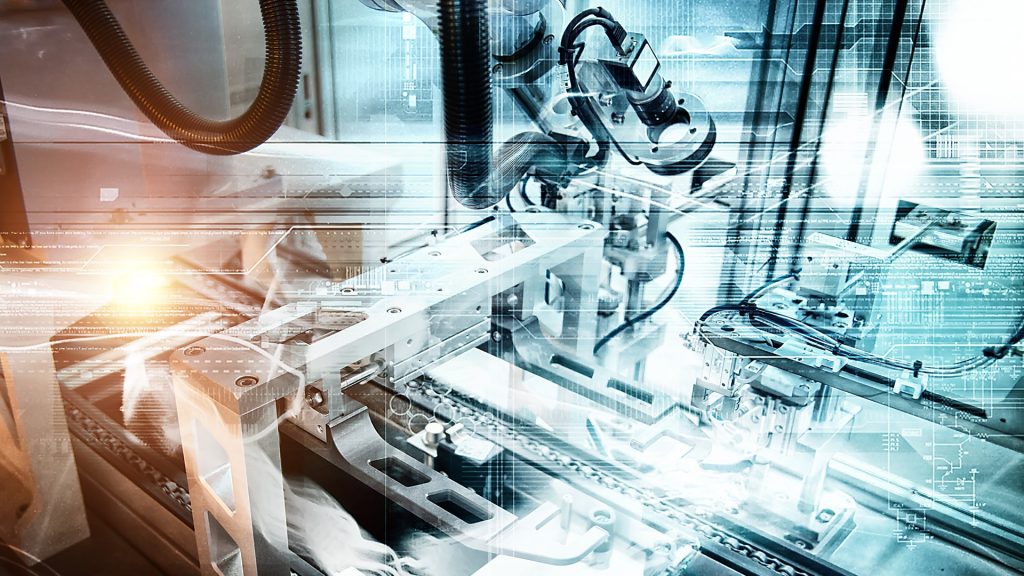
Jornada da transformação digital para indústrias
A Jornada da Transformação Digital para indústrias é um processo de evolução tecnológica e produtiva que visa modernizar as operações e impulsionar a competitividade das empresas. É um caminho gradual, onde as indústrias incorporam novas tecnologias e práticas para se adaptar às demandas do mercado e aos avanços tecnológicos.
A Cast group oferece uma consultoria completa para apoiar os clientes na jornada da digitalização, estabelecendo escopo de projeto, road maps, definição das tecnologias e muito mais.
A jornada pode variar de empresa para empresa, mas geralmente envolve as seguintes etapas:
- Diagnóstico: Avaliação da situação atual da empresa, identificando pontos fortes, fracos e oportunidades de melhoria.
- Elaboração da estratégia: Definição dos objetivos da transformação digital e do roadmap para alcançá-los.
- Implementação: Adoção de novas tecnologias e ferramentas, como IoT, inteligência artificial, big data e automação.
- Integração: Conexão de sistemas e dados para criar uma visão holística da operação.
- Otimização: Melhoria contínua dos processos e adaptação às novas tecnologias.
Aumento da eficiência e produtividade
- Otimização de processos: Automatização de tarefas repetitivas e integração de sistemas, resultando em menor tempo de execução e redução de erros.
- Melhoria da gestão da cadeia de suprimentos: Planejamento mais preciso da produção, redução de estoques e otimização da logística.
- Manutenção preditiva: Utilização de dados para prever falhas em equipamentos e realizar manutenções de forma proativa, evitando paradas não planejadas.
Inovação e desenvolvimento de novos produtos e serviços
- Análise de dados: Identificação de tendências de mercado e necessidades dos clientes, permitindo o desenvolvimento de produtos e serviços mais personalizados.
- Colaboração em tempo real: Facilitação da comunicação e do compartilhamento de informações entre equipes, acelerando o processo de desenvolvimento.
- Novos modelos de negócios: Criação de novas fontes de receita e expansão para novos mercados.
Melhoria da qualidade e satisfação do cliente
- Controle de qualidade: Monitoramento em tempo real dos processos e identificação de desvios, garantindo a qualidade dos produtos e serviços.
- Personalização: Oferecimento de produtos e serviços personalizados de acordo com as necessidades e preferências de cada cliente.
- Atendimento ao cliente mais eficiente: Utilização de ferramentas digitais para agilizar o atendimento e resolver problemas com mais rapidez.
Redução de custos
- Otimização do consumo de energia: Utilização de sistemas de gestão de energia para identificar e reduzir o consumo em áreas ineficientes.
- Redução de custos com papel e armazenamento: Digitalização de documentos e processos, eliminando a necessidade de armazenamento físico.
- Minimização de desperdícios: Otimização da utilização de matérias-primas e redução de retrabalho.
Outras vantagens
- Maior agilidade na tomada de decisões: Acesso a dados em tempo real e ferramentas de análise para tomada de decisões mais rápidas e assertivas.
- Aumento da segurança: Proteção de dados e sistemas contra ameaças cibernéticas.
- Atração e retenção de talentos: Criação de um ambiente de trabalho mais moderno e inovador, atraindo profissionais qualificados.
Em resumo, a jornada da transformação digital nas indústrias oferece uma série de benefícios que vão além da simples automatização de processos. Ela permite que as empresas se tornem mais competitivas, inovadoras e eficientes, garantindo sua sustentabilidade a longo prazo.
Plataformas MES
O que é um Sistema MES?
Um Sistema de Execução da Manufatura, ou MES (Manufacturing Execution System), é uma ferramenta de software que atua como um elo entre o planejamento da produção e o chão de fábrica. Ele oferece um controle preciso e em tempo real de todos os processos produtivos, desde a emissão de uma ordem até o embarque do produto final.
A implementação de um MES traz uma série de benefícios que podem transformar a forma como sua indústria opera:
- Aumento da eficiência: O MES otimiza o fluxo de trabalho, reduzindo tempos de setup, paradas de máquina e retrabalho.
- Melhoria da qualidade: Através do controle rigoroso dos processos, o MES garante a conformidade dos produtos com os padrões estabelecidos.
- Redução de custos: A otimização dos processos e a diminuição de desperdícios resultam em uma redução significativa dos custos operacionais.
- Tomada de decisões mais assertivas: O MES fornece dados precisos e em tempo real, permitindo que os gestores tomem decisões mais estratégicas e baseadas em fatos.
- Maior visibilidade: O MES oferece uma visão completa de toda a cadeia produtiva, facilitando o acompanhamento do desempenho e a identificação de gargalos.
- Integração com outros sistemas: O MES pode ser integrado a outros sistemas, como ERP e SCM, proporcionando uma gestão integrada da empresa.
Um MES permite:
- Monitoramento em tempo real: Acompanhar o status das ordens de produção, o desempenho das máquinas e a localização dos materiais.
- Coleta de dados: Capturar dados de produção, como tempo de ciclo, quantidade produzida, defeitos e paradas.
- Gerenciamento de qualidade: Controlar os processos de inspeção e garantir a qualidade dos produtos.
- Gerenciamento de manutenção: Programar e acompanhar as atividades de manutenção preventiva e corretiva.
- Gerenciamento de recursos: Otimizar o uso de recursos como mão de obra, máquinas e materiais.
- Geração de relatórios: Produzir relatórios personalizados para análise e tomada de decisão.
A implementação de um MES é um investimento estratégico para qualquer indústria que busca aumentar sua eficiência, qualidade e competitividade. Ao oferecer uma visão completa e em tempo real da produção, o MES permite que as empresas identifiquem oportunidades de melhoria, reduzam custos e garantam a satisfação dos clientes.
Projeto e implementação de células robotizadas.
O que é uma célula robotizada?
Uma célula robotizada é um sistema de automação industrial configurado de forma independente, composto por um ou mais robôs industriais e outros equipamentos periféricos, como transportadores, sensores e ferramentas. Essa célula é projetada para executar tarefas específicas dentro de um processo de produção, aumentando a eficiência, a precisão e a qualidade dos produtos.
Em resumo, uma célula robotizada é uma estação de trabalho automatizada que utiliza robôs para realizar tarefas repetitivas e complexas.
Uma célula robotizada funciona de forma integrada, com cada componente desempenhando um papel crucial:
- Robô industrial: É o elemento central, responsável por executar os movimentos e tarefas programadas.
- Controlador: Envia comandos ao robô e coordena as ações de todos os componentes da célula.
- Ferramentas: São acopladas ao robô para realizar diferentes tarefas, como soldagem, pintura, montagem, etc.
- Sensores: Coletam dados sobre o ambiente e o processo, permitindo que o robô ajuste suas ações em tempo real.
- Transportadores: Movem peças e materiais dentro da célula, alimentando o robô e removendo as peças acabadas.
A configuração de uma célula robotizada pode variar muito dependendo da aplicação. No entanto, alguns tipos comuns incluem:
- Célula de soldagem: Utilizada para realizar soldagens de alta precisão e repetibilidade, em diversas indústrias, como automotiva e metalúrgica.
- Célula de pintura: Aplica tintas e revestimentos em peças de forma uniforme e eficiente, garantindo um acabamento de alta qualidade.
- Célula de montagem: Realiza a montagem de componentes eletrônicos, mecânicos e outros produtos, com alta velocidade e precisão.
- Célula de paletização: Organiza produtos em paletes de forma automatizada, otimizando o espaço de armazenamento e facilitando o transporte.
- Célula de usinagem: Realiza operações de usinagem, como corte, furação e fresamento, com alta precisão e repetibilidade.
A implementação de células robotizadas nas indústrias traz diversos benefícios, como:
- Aumento da produtividade: Os robôs podem trabalhar continuamente, sem interrupções, aumentando a produção e reduzindo os custos.
- Melhora da qualidade: A alta precisão dos robôs garante produtos de alta qualidade, com menor número de defeitos.
- Redução de custos: A automação pode reduzir custos com mão de obra, materiais e desperdícios.
- Maior segurança: A realização de tarefas perigosas por robôs reduz o risco de acidentes de trabalho.
- Flexibilidade: As células robotizadas podem ser facilmente reconfiguradas para atender a diferentes produtos e volumes de produção.
Em resumo, as células robotizadas são uma ferramenta poderosa para aumentar a eficiência e a competitividade das empresas, transformando os processos de produção e abrindo caminho para a indústria 4.0.
Soluções em robótica móvel com AGV, AMR e LMR
A indústria está em constante evolução, buscando cada vez mais eficiência, produtividade e flexibilidade em seus processos. As soluções em robótica móvel surgem como uma resposta a essa demanda, oferecendo uma gama de benefícios para as empresas.
- AGV (Veículo Guiado Automaticamente): São robôs móveis programados para seguir um caminho pré-definido, geralmente utilizando guias no chão ou sinais magnéticos. Seus movimentos são mais restritos e sua programação é mais complexa.
- AMR (Robô Móvel Autônomo): Diferentemente dos AGVs, os AMRs possuem maior autonomia e flexibilidade. Utilizam sensores e softwares avançados para navegar em ambientes dinâmicos, evitando obstáculos e adaptando suas rotas em tempo real.
- LMR (Robô Móvel Logístico): É um termo mais abrangente que engloba tanto AGVs quanto AMRs, e pode incluir outros tipos de robôs utilizados em operações logísticas.
- Aumento da eficiência: Os robôs móveis podem realizar tarefas repetitivas e perigosas com maior precisão e velocidade, liberando os colaboradores para atividades que exigem maior criatividade e tomada de decisão.
- Redução de custos: A automatização de processos pode levar a uma redução significativa de custos operacionais, como mão de obra e erros humanos.
- Melhoria da segurança: Ao realizar tarefas perigosas, os robôs móveis contribuem para um ambiente de trabalho mais seguro para os colaboradores.
- Maior flexibilidade: Os AMRs, em particular, são altamente flexíveis e podem ser facilmente reconfigurados para atender às mudanças nas demandas de produção.
- Otimização do espaço: Os robôs móveis podem operar em espaços confinados e otimizar o fluxo de materiais dentro de um armazém ou fábrica.
- Aumento da produtividade: Com processos mais eficientes e precisos, a produtividade geral da empresa pode ser significativamente aumentada.
As soluções em robótica móvel podem ser aplicadas em diversas áreas da indústria, como:
- Logística: Transporte de materiais, picking e packing, gestão de estoque.
- Manufatura: Montagem de produtos, movimentação de peças, inspeção de qualidade.
- Saúde: Transporte de materiais médicos, desinfecção de ambientes.
- Varejo: Gestão de estoque, atendimento ao cliente.
As soluções em robótica móvel com AGV, AMR e LMR representam uma revolução na forma como as indústrias operam. Ao oferecer maior eficiência, flexibilidade e segurança, esses robôs estão transformando a maneira como as empresas produzem e entregam seus produtos.
Integração com SAP
O que é a Integração com SAP?
A integração com SAP consiste em conectar diferentes sistemas e softwares de uma empresa ao poderoso sistema de planejamento de recursos empresariais (ERP) SAP. Essa conexão permite que diversos processos, desde a produção até a contabilidade, sejam automatizados e centralizados em uma única plataforma.
A integração com SAP traz uma série de vantagens para as indústrias, como:
- Otimização de processos: A automatização de fluxos de trabalho reduz erros manuais, agiliza a tomada de decisões e aumenta a eficiência operacional.
- Visibilidade total: Ao centralizar os dados em uma única plataforma, as empresas obtêm uma visão completa e em tempo real de suas operações, facilitando o acompanhamento do desempenho e a identificação de oportunidades de melhoria.
- Melhoria da tomada de decisões: Com dados precisos e atualizados, as empresas podem tomar decisões mais estratégicas e baseadas em evidências, o que impulsiona o crescimento e a competitividade.
- Redução de custos: A eliminação de processos manuais e a otimização da cadeia de suprimentos contribuem para a redução de custos operacionais.
- Conformidade regulatória: O SAP oferece ferramentas para garantir o cumprimento de normas e regulamentações específicas do setor, minimizando riscos e multas.
- Escalabilidade: A plataforma SAP é altamente escalável, permitindo que as empresas acompanhem o crescimento do negócio e adaptem seus sistemas às novas demandas.
A integração com SAP pode ser aplicada em diversos cenários, como:
- Gerenciamento da cadeia de suprimentos: Integração com sistemas de logística, transporte e gestão de estoque para otimizar a distribuição de produtos e reduzir custos.
- Gerenciamento financeiro: Integração com sistemas de contabilidade, contas a pagar e receber para automatizar processos financeiros e gerar relatórios precisos.
- Gerenciamento de recursos humanos: Integração com sistemas de folha de pagamento, gestão de benefícios e recrutamento para otimizar a gestão de talentos.
- Gerenciamento da produção: Integração com sistemas de planejamento de produção, controle de qualidade e manutenção para otimizar os processos produtivos.
- Comércio eletrônico: Integração com plataformas de e-commerce para sincronizar informações de produtos, estoque e pedidos.
A integração com SAP é uma solução poderosa para empresas que buscam otimizar seus processos, aumentar a eficiência e tomar decisões mais estratégicas. Ao conectar diferentes sistemas em uma única plataforma, as empresas podem obter uma visão completa de suas operações e alcançar um novo nível de competitividade.
Soluções com internet das coisas | IoT
A Internet das Coisas (IoT) revolucionou a forma como as indústrias operam, conectando dispositivos e máquinas para coletar e analisar dados em tempo real. Mas o que isso significa na prática?
Soluções com IoT são sistemas que utilizam sensores, softwares e a internet para monitorar e controlar equipamentos, processos e ambientes industriais. Esses sistemas permitem uma visibilidade completa das operações, desde a linha de produção até a logística, gerando insights valiosos para a tomada de decisões estratégicas.
- Otimização de processos: A IoT permite identificar gargalos, ineficiências e oportunidades de melhoria nos processos produtivos, resultando em maior eficiência e redução de custos.
- Manutenção preditiva: Ao monitorar o estado dos equipamentos em tempo real, é possível prever falhas e realizar a manutenção de forma proativa, evitando paradas não planejadas e aumentando a vida útil dos ativos.
- Gerenciamento de energia: A IoT permite otimizar o consumo de energia, identificando oportunidades de redução e economizando recursos.
- Melhoria da qualidade: Através do monitoramento constante dos processos, é possível garantir a qualidade dos produtos e reduzir a quantidade de defeitos.
- Segurança: A IoT pode ser utilizada para monitorar a segurança de ambientes industriais, identificando riscos e prevenindo acidentes.
- Agilidade: A tomada de decisões mais rápida e precisa, baseada em dados em tempo real, permite uma maior agilidade na resposta a mudanças no mercado e nas demandas dos clientes.
- Monitoramento de condições ambientais: Sensores monitoram temperatura, umidade e outros parâmetros em ambientes de produção, garantindo a qualidade dos produtos e a segurança dos colaboradores.
- Gerenciamento de estoques: Sensores monitoram os níveis de estoque, permitindo a reposição automática de materiais e evitando a falta de insumos.
- Rastreamento de ativos: A IoT permite rastrear a localização de equipamentos e materiais em tempo real, otimizando a logística e reduzindo perdas.
- Automação de processos: A IoT permite automatizar tarefas repetitivas e perigosas, aumentando a produtividade e a segurança dos colaboradores.
Em resumo, as soluções com IoT oferecem às indústrias uma série de benefícios, como maior eficiência, redução de custos, melhoria da qualidade e maior segurança. Ao transformar dados em insights acionáveis, a IoT impulsiona a indústria para um futuro mais inteligente e conectado.
Soluções especiais em automação industrial
O que são Soluções Especiais em Automação Industrial?
Em um mundo cada vez mais tecnológico, a indústria busca constantemente otimizar seus processos para aumentar a produtividade, reduzir custos e garantir a qualidade dos produtos. As soluções especiais em automação industrial são projetos personalizados, desenvolvidos sob medida para atender às necessidades específicas de cada empresa.
Essas soluções vão além dos sistemas de automação convencionais, oferecendo um leque de possibilidades para automatizar tarefas complexas e repetitivas, desde a linha de produção até a gestão de dados.
As soluções especiais em automação industrial envolvem a integração de diversos componentes e tecnologias, como:
- Robôs industriais: Realizam tarefas com alta precisão e velocidade, liberando os colaboradores para atividades que exigem maior criatividade e raciocínio.
- Sistemas de visão: Utilizam câmeras e softwares para inspecionar produtos, identificar defeitos e garantir a qualidade.
- Controladores lógicos programáveis (CLPs): Controlam e coordenam todos os elementos do processo de produção.
- Interfaces homem-máquina (IHMs): Permitem que os operadores monitorem e controlem os processos de forma intuitiva.
- Softwares de gestão: Coletam e analisam dados para otimizar a produção e a manutenção.
- Aumento da produtividade: Automação de tarefas repetitivas e redução do tempo de ciclo.
- Melhora da qualidade: Maior precisão e consistência nos processos, reduzindo a quantidade de defeitos.
- Redução de custos: Otimização do uso de recursos, diminuição de desperdícios e maior eficiência energética.
- Flexibilidade: Adaptação rápida a mudanças nas demandas do mercado e novos produtos.
- Segurança: Redução de riscos de acidentes e doenças ocupacionais.
- Otimização da manutenção: Monitoramento em tempo real do estado dos equipamentos e previsão de falhas.
- Linhas de montagem: Automação de tarefas como soldagem, pintura e embalagem.
- Máquinas especiais: Desenvolvimento de máquinas personalizadas para processos específicos.
- Células robotizadas: Integração de robôs com outros equipamentos para realizar tarefas complexas.
- Sistemas de visão: Inspeção de peças, leitura de códigos de barras e controle de qualidade.
As soluções especiais em automação industrial são a chave para a modernização e a competitividade das empresas. Ao oferecer um alto grau de personalização e flexibilidade, essas soluções permitem que as indústrias otimizem seus processos, aumentem a produtividade e garantam a qualidade de seus produtos.
Soluções com tecnologia RFID
O que é RFID?
RFID, sigla para Radio Frequency Identification, ou Identificação por Radiofrequência em português, é uma tecnologia que utiliza ondas de rádio para identificar e rastrear objetos. Essa tecnologia funciona através de etiquetas eletrônicas, chamadas de tags, que contêm chips capazes de armazenar informações e uma antena para receber e transmitir sinais. Quando uma tag se aproxima de um leitor RFID, ela é energizada pela onda de rádio e envia de volta as informações armazenadas.
Na indústria, o RFID tem se mostrado uma ferramenta extremamente útil para diversas aplicações, como:
- Gerenciamento de estoque: Ao marcar cada item com uma tag RFID, as empresas podem rastrear o movimento de produtos dentro do armazém, desde a entrada até a saída, otimizando a gestão de estoque e reduzindo perdas.
- Controle de acesso: O RFID pode ser utilizado para controlar o acesso de pessoas e veículos a áreas restritas, aumentando a segurança e o controle.
- Rastreamento de ativos: Equipamentos, ferramentas e outros ativos podem ser rastreados com RFID, facilitando a localização e evitando perdas.
- Automação de processos: O RFID pode ser integrado a sistemas de automação para otimizar processos como a linha de produção, a embalagem e a expedição.
- Gerenciamento da cadeia de suprimentos: A tecnologia permite rastrear produtos ao longo de toda a cadeia de suprimentos, desde a fabricação até o consumidor final, garantindo a rastreabilidade e a segurança dos produtos.
A tecnologia RFID pode resolver diversos problemas enfrentados pelas indústrias, como:
- Redução de erros: A automatização do processo de identificação e rastreamento reduz a incidência de erros manuais, como a leitura incorreta de códigos de barras.
- Aumento da eficiência: O RFID permite otimizar processos, reduzir o tempo de busca por itens e aumentar a produtividade.
- Melhoria da precisão: As informações coletadas pelo RFID são precisas e em tempo real, permitindo um melhor controle dos processos.
- Maior visibilidade: A tecnologia proporciona uma visão completa da cadeia de suprimentos, facilitando a tomada de decisões e a resolução de problemas.
- Redução de custos: A otimização dos processos e a redução de perdas e erros contribuem para a redução dos custos operacionais.
Existem diversos tipos de tags RFID, que se diferenciam em termos de frequência, alcance, memória e custo. Os principais tipos são:
- Tags de baixa frequência: Utilizadas em aplicações de curto alcance, como sistemas de controle de acesso e identificação de animais.
- Tags de alta frequência: Oferecem maior alcance e capacidade de armazenamento, sendo utilizadas em aplicações como gestão de estoque e rastreamento de ativos.
- Tags de ultra alta frequência: Possuem maior alcance e velocidade de leitura, sendo ideais para aplicações que exigem alta performance, como logística e transporte.
O RFID é uma tecnologia versátil e poderosa que pode trazer inúmeros benefícios para as indústrias. Ao automatizar processos, aumentar a precisão e oferecer maior visibilidade, o RFID contribui para a otimização da operação e a melhoria da competitividade das empresas.
Jornada da transformação digital para indústrias.
A Jornada da Transformação Digital para indústrias é um processo de evolução tecnológica e produtiva que visa modernizar as operações e impulsionar a competitividade das empresas. É um caminho gradual, onde as indústrias incorporam novas tecnologias e práticas para se adaptar às demandas do mercado e aos avanços tecnológicos.
A Cast group oferece uma consultoria completa para apoiar os clientes na jornada da digitalização, estabelecendo escopo de projeto, road maps, definição das tecnologias e muito mais.
Por que a transformação digital é importante para as indústrias?
- Aumento da eficiência: Automação de processos, otimização da cadeia de suprimentos e redução de custos operacionais.
- Inovação: Desenvolvimento de novos produtos e serviços, além de modelos de negócios mais personalizados e flexíveis.
- Melhoria da qualidade: Controle de qualidade mais rigoroso e garantia de produtos e serviços que atendam às expectativas
dos clientes. - Agilidade: Tomada de decisões mais rápidas e assertivas com base em dados em tempo real.
- Competitividade: Diferenciação no mercado e capacidade de responder rapidamente às mudanças.
Aumento da Eficiência e Produtividade
- Otimização de processos: Automatização de tarefas repetitivas e integração de sistemas, resultando em menor tempo de
execução e redução de erros. - Melhoria da gestão da cadeia de suprimentos: Planejamento mais preciso da produção, redução de estoques e otimização da
logística. - Manutenção preditiva: Utilização de dados para prever falhas em equipamentos e realizar manutenções de forma proativa,
evitando paradas não planejadas.
Inovação e Desenvolvimento de Novos Produtos e Serviços
- Análise de dados: Identificação de tendências de mercado e necessidades dos clientes, permitindo o desenvolvimento de
produtos e serviços mais personalizados. - Colaboração em tempo real: Facilitação da comunicação e do compartilhamento de informações entre equipes, acelerando o
processo de desenvolvimento. - Novos modelos de negócios: Criação de novas fontes de receita e expansão para novos mercados.
Melhoria da Qualidade e Satisfação do Cliente
- Controle de qualidade: Monitoramento em tempo real dos processos e identificação de desvios, garantindo a qualidade dos
produtos e serviços. - Personalização: Oferecimento de produtos e serviços personalizados de acordo com as necessidades e preferências de cada
cliente. - Atendimento ao cliente mais eficiente: Utilização de ferramentas digitais para agilizar o atendimento e resolver problemas com
mais rapidez.
Redução de Custos
- Otimização do consumo de energia: Utilização de sistemas de gestão de energia para identificar e reduzir o consumo em
áreas ineficientes. - Redução de custos com papel e armazenamento: Digitalização de documentos e processos, eliminando a necessidade de
armazenamento físico. - Minimização de desperdícios: Otimização da utilização de matérias-primas e redução de retrabalho.
Outras Vantagens
- Maior agilidade na tomada de decisões: Acesso a dados em tempo real e ferramentas de análise para tomada de decisões
mais rápidas e assertivas. - Aumento da segurança: Proteção de dados e sistemas contra ameaças cibernéticas.
- Atração e retenção de talentos: Criação de um ambiente de trabalho mais moderno e inovador, atraindo profissionais
qualificados.
Quais as etapas de uma jornada de transformação digital?
A jornada pode variar de empresa para empresa, mas geralmente envolve as seguintes etapas:
- Diagnóstico: Avaliação da situação atual da empresa, identificando pontos fortes, fracos e oportunidades de melhoria.
- Elaboração da estratégia: Definição dos objetivos da transformação digital e do roadmap para alcançá-los.
- Implementação: Adoção de novas tecnologias e ferramentas, como IoT, inteligência artificial, big data e automação.
- Integração: Conexão de sistemas e dados para criar uma visão holística da operação.
- Otimização: Melhoria contínua dos processos e adaptação às novas tecnologias.
Em resumo, a jornada da transformação digital nas indústrias oferece uma série de benefícios que vão além da simples
automatização de processos. Ela permite que as empresas se tornem mais competitivas, inovadoras e eficientes, garantindo sua
sustentabilidade a longo prazo.
Plataformas MES
Um Sistema de Execução da Manufatura, ou MES (Manufacturing Execution System), é uma ferramenta de software que atua
como um elo entre o planejamento da produção e o chão de fábrica. Ele oferece um controle preciso e em tempo real de todos os
processos produtivos, desde a emissão de uma ordem até o embarque do produto final.
Por que implementar um MES na sua indústria?
A implementação de um MES traz uma série de benefícios que podem transformar a forma como sua indústria opera:
- Aumento da eficiência: O MES otimiza o fluxo de trabalho, reduzindo tempos de setup, paradas de máquina e retrabalho.
- Melhoria da qualidade: Através do controle rigoroso dos processos, o MES garante a conformidade dos produtos com os
padrões estabelecidos. - Redução de custos: A otimização dos processos e a diminuição de desperdícios resultam em uma redução significativa dos
custos operacionais. - Tomada de decisões mais assertivas: O MES fornece dados precisos e em tempo real, permitindo que os gestores tomem
decisões mais estratégicas e baseadas em fatos. - Maior visibilidade: O MES oferece uma visão completa de toda a cadeia produtiva, facilitando o acompanhamento do
desempenho e a identificação de gargalos. - Integração com outros sistemas: O MES pode ser integrado a outros sistemas, como ERP e SCM, proporcionando uma gestão
integrada da empresa.
Como funciona um MES na prática?
Um MES permite:
- Monitoramento em tempo real: Acompanhar o status das ordens de produção, o desempenho das máquinas e a localização
dos materiais. - Coleta de dados: Capturar dados de produção, como tempo de ciclo, quantidade produzida, defeitos e paradas.
- Gerenciamento de qualidade: Controlar os processos de inspeção e garantir a qualidade dos produtos.
- Gerenciamento de manutenção: Programar e acompanhar as atividades de manutenção preventiva e corretiva.
- Gerenciamento de recursos: Otimizar o uso de recursos como mão de obra, máquinas e materiais.
- Geração de relatórios: Produzir relatórios personalizados para análise e tomada de decisão.
A implementação de um MES é um investimento estratégico para qualquer indústria que busca aumentar sua eficiência, qualidade
e competitividade. Ao oferecer uma visão completa e em tempo real da produção, o MES permite que as empresas identifiquem
oportunidades de melhoria, reduzam custos e garantam a satisfação dos clientes.
Projeto e implementação de células robotizadas.
Uma célula robotizada é um sistema de automação industrial configurado de forma independente, composto por um ou mais
robôs industriais e outros equipamentos periféricos, como transportadores, sensores e ferramentas. Essa célula é projetada
para executar tarefas específicas dentro de um processo de produção, aumentando a eficiência, a precisão e a qualidade dos
produtos.
Em resumo, uma célula robotizada é uma estação de trabalho automatizada que utiliza robôs para realizar tarefas repetitivas
e complexas.
Projeto e Implementação de Células Robotizadas.
Uma célula robotizada é um sistema de automação industrial configurado de forma independente, composto por um ou mais
robôs industriais e outros equipamentos periféricos, como transportadores, sensores e ferramentas. Essa célula é projetada
para executar tarefas específicas dentro de um processo de produção, aumentando a eficiência, a precisão e a qualidade dos
produtos.
Em resumo, uma célula robotizada é uma estação de trabalho automatizada que utiliza robôs para realizar tarefas repetitivas
e complexas.
Como funciona uma célula robotizada?
Uma célula robotizada funciona de forma integrada, com cada componente desempenhando um papel crucial:
- Robô industrial: É o elemento central, responsável por executar os movimentos e tarefas programadas.
- Controlador: Envia comandos ao robô e coordena as ações de todos os componentes da célula.
- Ferramentas: São acopladas ao robô para realizar diferentes tarefas, como soldagem, pintura, montagem, etc.
- Sensores: Coletam dados sobre o ambiente e o processo, permitindo que o robô ajuste suas ações em tempo real.
- Transportadores: Movem peças e materiais dentro da célula, alimentando o robô e removendo as peças acabadas.
Quais os tipos de células robotizadas?
A configuração de uma célula robotizada pode variar muito dependendo da aplicação. No entanto, alguns tipos comuns incluem:
- Célula de soldagem: Utilizada para realizar soldagens de alta precisão e repetibilidade, em diversas indústrias, como automotiva e metalúrgica.
- Célula de pintura: Aplica tintas e revestimentos em peças de forma uniforme e eficiente, garantindo um acabamento de alta qualidade.
- Célula de montagem: Realiza a montagem de componentes eletrônicos, mecânicos e outros produtos, com alta velocidade e precisão.
- Célula de paletização: Organiza produtos em paletes de forma automatizada, otimizando o espaço de armazenamento e facilitando o transporte.
- Célula de usinagem: Realiza operações de usinagem, como corte, furação e fresamento, com alta precisão e repetibilidade.
Benefícios da implementação de células robotizadas
A implementação de células robotizadas nas indústrias traz diversos benefícios, como:
- Aumento da produtividade: Os robôs podem trabalhar continuamente, sem interrupções, aumentando a produção e reduzindo os custos.
- Melhora da qualidade: A alta precisão dos robôs garante produtos de alta qualidade, com menor número de defeitos.
- Redução de custos: A automação pode reduzir custos com mão de obra, materiais e desperdícios.
- Maior segurança: A realização de tarefas perigosas por robôs reduz o risco de acidentes de trabalho.
- Flexibilidade: As células robotizadas podem ser facilmente reconfiguradas para atender a diferentes produtos e volumes de produção.
Em resumo, as células robotizadas são uma ferramenta poderosa para aumentar a eficiência e a competitividade das empresas, transformando os processos de produção e abrindo caminho para a indústria 4.0.
Gostaria de saber mais sobre algum tipo específico de célula robotizada ou sobre os seus benefícios para um determinado setor industrial?
Soluções em robótica móvel com AGV, AMR e LMR.
A indústria está em constante evolução, buscando cada vez mais eficiência, produtividade e flexibilidade em seus processos. As soluções em robótica móvel surgem como uma resposta a essa demanda, oferecendo uma gama de benefícios para as empresas.
O que são AGV, AMR e LMR?
- AGV (Veículo Guiado Automaticamente): São robôs móveis programados para seguir um caminho pré-definido, geralmente
utilizando guias no chão ou sinais magnéticos. Seus movimentos são mais restritos e sua programação é mais complexa. - AMR (Robô Móvel Autônomo): Diferentemente dos AGVs, os AMRs possuem maior autonomia e flexibilidade. Utilizam
sensores e softwares avançados para navegar em ambientes dinâmicos, evitando obstáculos e adaptando suas rotas em
tempo real. - LMR (Robô Móvel Logístico): É um termo mais abrangente que engloba tanto AGVs quanto AMRs, e pode incluir outros tipos
de robôs utilizados em operações logísticas.
Benefícios para as Indústrias:
- Aumento da eficiência: Os robôs móveis podem realizar tarefas repetitivas e perigosas com maior precisão e velocidade,
liberando os colaboradores para atividades que exigem maior criatividade e tomada de decisão. - Redução de custos: A automatização de processos pode levar a uma redução significativa de custos operacionais, como mão
de obra e erros humanos. - Melhoria da segurança: Ao realizar tarefas perigosas, os robôs móveis contribuem para um ambiente de trabalho mais seguro
para os colaboradores. - Maior flexibilidade: Os AMRs, em particular, são altamente flexíveis e podem ser facilmente reconfigurados para atender às
mudanças nas demandas de produção. - Otimização do espaço: Os robôs móveis podem operar em espaços confinados e otimizar o fluxo de materiais dentro de um
armazém ou fábrica. - Aumento da produtividade: Com processos mais eficientes e precisos, a produtividade geral da empresa pode ser
significativamente aumentada.
Aplicações na Indústria:
As soluções em robótica móvel podem ser aplicadas em diversas áreas da indústria, como:
- Logística: Transporte de materiais, picking e packing, gestão de estoque.
- Manufatura: Montagem de produtos, movimentação de peças, inspeção de qualidade.
- Saúde: Transporte de materiais médicos, desinfecção de ambientes.
- Varejo: Gestão de estoque, atendimento ao cliente.
As soluções em robótica móvel com AGV, AMR e LMR representam uma revolução na forma como as indústrias operam. Ao
oferecer maior eficiência, flexibilidade e segurança, esses robôs estão transformando a maneira como as empresas produzem e
entregam seus produtos.
Integração com SAP
A integração com SAP consiste em conectar diferentes sistemas e softwares de uma empresa ao poderoso sistema de
planejamento de recursos empresariais (ERP) SAP. Essa conexão permite que diversos processos, desde a produção até a
contabilidade, sejam automatizados e centralizados em uma única plataforma.
O que é a Integração com SAP?
A integração com SAP consiste em conectar diferentes sistemas e softwares de uma empresa ao poderoso sistema de
planejamento de recursos empresariais (ERP) SAP. Essa conexão permite que diversos processos, desde a produção até a
contabilidade, sejam automatizados e centralizados em uma única plataforma.
Benefícios para as Indústrias:
A integração com SAP traz uma série de vantagens para as indústrias, como:
- Otimização de processos: A automatização de fluxos de trabalho reduz erros manuais, agiliza a tomada de decisões e
aumenta a eficiência operacional. - Visibilidade total: Ao centralizar os dados em uma única plataforma, as empresas obtêm uma visão completa e em tempo real
de suas operações, facilitando o acompanhamento do desempenho e a identificação de oportunidades de melhoria. - Melhoria da tomada de decisões: Com dados precisos e atualizados, as empresas podem tomar decisões mais estratégicas e
baseadas em evidências, o que impulsiona o crescimento e a competitividade. - Redução de custos: A eliminação de processos manuais e a otimização da cadeia de suprimentos contribuem para a redução
de custos operacionais. - Conformidade regulatória: O SAP oferece ferramentas para garantir o cumprimento de normas e regulamentações específicas
do setor, minimizando riscos e multas. - Escalabilidade: A plataforma SAP é altamente escalável, permitindo que as empresas acompanhem o crescimento do negócio
e adaptem seus sistemas às novas demandas.
Como a Integração com SAP funciona na Prática?
A integração com SAP pode ser aplicada em diversos cenários, como:
- Gerenciamento da cadeia de suprimentos: Integração com sistemas de logística, transporte e gestão de estoque para otimizar
a distribuição de produtos e reduzir custos. - Gerenciamento financeiro: Integração com sistemas de contabilidade, contas a pagar e receber para automatizar processos
financeiros e gerar relatórios precisos. - Gerenciamento de recursos humanos: Integração com sistemas de folha de pagamento, gestão de benefícios e recrutamento
para otimizar a gestão de talentos. - Gerenciamento da produção: Integração com sistemas de planejamento de produção, controle de qualidade e manutenção
para otimizar os processos produtivos. - Comércio eletrônico: Integração com plataformas de e-commerce para sincronizar informações de produtos, estoque e
pedidos.
A integração com SAP é uma solução poderosa para empresas que buscam otimizar seus processos, aumentar a eficiência e
tomar decisões mais estratégicas. Ao conectar diferentes sistemas em uma única plataforma, as empresas podem obter uma
visão completa de suas operações e alcançar um novo nível de competitividade.
Soluções com internet das coisas | IoT
A Internet das Coisas (IoT) revolucionou a forma como as indústrias operam, conectando dispositivos e máquinas para coletar e analisar dados em tempo real. Mas o que isso significa na prática?
Soluções com IoT são sistemas que utilizam sensores, softwares e a internet para monitorar e controlar equipamentos, processos e ambientes industriais. Esses sistemas permitem uma visibilidade completa das operações, desde a linha de produção até a logística, gerando insights valiosos para a tomada de decisões estratégicas.
Quais os benefícios para a indústria?
- Otimização de processos: A IoT permite identificar gargalos, ineficiências e oportunidades de melhoria nos processos
produtivos, resultando em maior eficiência e redução de custos. - Manutenção preditiva: Ao monitorar o estado dos equipamentos em tempo real, é possível prever falhas e realizar a
manutenção de forma proativa, evitando paradas não planejadas e aumentando a vida útil dos ativos. - Gerenciamento de energia: A IoT permite otimizar o consumo de energia, identificando oportunidades de redução e
economizando recursos. - Melhoria da qualidade: Através do monitoramento constante dos processos, é possível garantir a qualidade dos produtos e
reduzir a quantidade de defeitos. - Segurança: A IoT pode ser utilizada para monitorar a segurança de ambientes industriais, identificando riscos e prevenindo
acidentes. - Agilidade: A tomada de decisões mais rápida e precisa, baseada em dados em tempo real, permite uma maior agilidade na
resposta a mudanças no mercado e nas demandas dos clientes.
Exemplos de aplicações da IoT na indústria:
- Monitoramento de condições ambientais: Sensores monitoram temperatura, umidade e outros parâmetros em ambientes de
produção, garantindo a qualidade dos produtos e a segurança dos colaboradores. - Gerenciamento de estoques: Sensores monitoram os níveis de estoque, permitindo a reposição automática de materiais e
evitando a falta de insumos. - Rastreamento de ativos: A IoT permite rastrear a localização de equipamentos e materiais em tempo real, otimizando a
logística e reduzindo perdas. - Automação de processos: A IoT permite automatizar tarefas repetitivas e perigosas, aumentando a produtividade e a
segurança dos colaboradores.
Em resumo, as soluções com IoT oferecem às indústrias uma série de benefícios, como maior eficiência, redução de custos,
melhoria da qualidade e maior segurança. Ao transformar dados em insights acionáveis, a IoT impulsiona a indústria para um
futuro mais inteligente e conectado.
Soluções especiais em automação industrial.
Em um mundo cada vez mais tecnológico, a indústria busca constantemente otimizar seus processos para aumentar a
produtividade, reduzir custos e garantir a qualidade dos produtos. As soluções especiais em automação industrial são projetos
personalizados, desenvolvidos sob medida para atender às necessidades específicas de cada empresa.
Essas soluções vão além dos sistemas de automação convencionais, oferecendo um leque de possibilidades para automatizar
tarefas complexas e repetitivas, desde a linha de produção até a gestão de dados.
O que são Soluções Especiais em Automação Industrial?
Em um mundo cada vez mais tecnológico, a indústria busca constantemente otimizar seus processos para aumentar a
produtividade, reduzir custos e garantir a qualidade dos produtos. As soluções especiais em automação industrial são projetos
personalizados, desenvolvidos sob medida para atender às necessidades específicas de cada empresa.
Essas soluções vão além dos sistemas de automação convencionais, oferecendo um leque de possibilidades para automatizar
tarefas complexas e repetitivas, desde a linha de produção até a gestão de dados.
Como funcionam e quais os benefícios?
As soluções especiais em automação industrial envolvem a integração de diversos componentes e tecnologias, como:
- Robôs industriais: Realizam tarefas com alta precisão e velocidade, liberando os colaboradores para atividades que exigem
maior criatividade e raciocínio. - Sistemas de visão: Utilizam câmeras e softwares para inspecionar produtos, identificar defeitos e garantir a qualidade.
- Controladores lógicos programáveis (CLPs): Controlam e coordenam todos os elementos do processo de produção.
- Interfaces homem-máquina (IHMs): Permitem que os operadores monitorem e controlem os processos de forma intuitiva.
- Softwares de gestão: Coletam e analisam dados para otimizar a produção e a manutenção.
Benefícios para as indústrias:
- Aumento da produtividade: Automação de tarefas repetitivas e redução do tempo de ciclo.
- Melhora da qualidade: Maior precisão e consistência nos processos, reduzindo a quantidade de defeitos.
- Redução de custos: Otimização do uso de recursos, diminuição de desperdícios e maior eficiência energética.
- Flexibilidade: Adaptação rápida a mudanças nas demandas do mercado e novos produtos.
- Segurança: Redução de riscos de acidentes e doenças ocupacionais.
- Otimização da manutenção: Monitoramento em tempo real do estado dos equipamentos e previsão de falhas.
Exemplos de aplicações:
- Linhas de montagem: Automação de tarefas como soldagem, pintura e embalagem.
- Máquinas especiais: Desenvolvimento de máquinas personalizadas para processos específicos.
- Células robotizadas: Integração de robôs com outros equipamentos para realizar tarefas complexas.
- Sistemas de visão: Inspeção de peças, leitura de códigos de barras e controle de qualidade.
As soluções especiais em automação industrial são a chave para a modernização e a competitividade das empresas. Ao oferecer
um alto grau de personalização e flexibilidade, essas soluções permitem que as indústrias otimizem seus processos, aumentem a
produtividade e garantam a qualidade de seus produtos.
Soluções com tecnologia RFID
RFID, sigla para Radio Frequency Identification, ou Identificação por Radiofrequência em português, é uma tecnologia que utiliza
ondas de rádio para identificar e rastrear objetos. Essa tecnologia funciona através de etiquetas eletrônicas, chamadas de tags,
que contêm chips capazes de armazenar informações e uma antena para receber e transmitir sinais. Quando uma tag se
aproxima de um leitor RFID, ela é energizada pela onda de rádio e envia de volta as informações armazenadas.
O que é RFID?
RFID, sigla para Radio Frequency Identification, ou Identificação por Radiofrequência em português, é uma tecnologia que utiliza
ondas de rádio para identificar e rastrear objetos. Essa tecnologia funciona através de etiquetas eletrônicas, chamadas de tags,
que contêm chips capazes de armazenar informações e uma antena para receber e transmitir sinais. Quando uma tag se
aproxima de um leitor RFID, ela é energizada pela onda de rádio e envia de volta as informações armazenadas.
Como o RFID funciona na indústria?
Na indústria, o RFID tem se mostrado uma ferramenta extremamente útil para diversas aplicações, como:
- Gerenciamento de estoque: Ao marcar cada item com uma tag RFID, as empresas podem rastrear o movimento de produtos
dentro do armazém, desde a entrada até a saída, otimizando a gestão de estoque e reduzindo perdas. - Controle de acesso: O RFID pode ser utilizado para controlar o acesso de pessoas e veículos a áreas restritas, aumentando a
segurança e o controle. - Rastreamento de ativos: Equipamentos, ferramentas e outros ativos podem ser rastreados com RFID, facilitando a localização
e evitando perdas. - Automação de processos: O RFID pode ser integrado a sistemas de automação para otimizar processos como a linha de
produção, a embalagem e a expedição. - Gerenciamento da cadeia de suprimentos: A tecnologia permite rastrear produtos ao longo de toda a cadeia de suprimentos,
desde a fabricação até o consumidor final, garantindo a rastreabilidade e a segurança dos produtos.
Quais problemas o RFID pode resolver?
A tecnologia RFID pode resolver diversos problemas enfrentados pelas indústrias, como:
- Redução de erros: A automatização do processo de identificação e rastreamento reduz a incidência de erros manuais,
como a leitura incorreta de códigos de barras. - Aumento da eficiência: O RFID permite otimizar processos, reduzir o tempo de busca por itens e aumentar a
produtividade. - Melhoria da precisão: As informações coletadas pelo RFID são precisas e em tempo real, permitindo um melhor controle
dos processos. - Maior visibilidade: A tecnologia proporciona uma visão completa da cadeia de suprimentos, facilitando a tomada de
decisões e a resolução de problemas. - Redução de custos: A otimização dos processos e a redução de perdas e erros contribuem para a redução dos custos
operacionais.
Tipos de tags RFID:
Existem diversos tipos de tags RFID, que se diferenciam em termos de frequência, alcance, memória e custo. Os principais
tipos são:
- Tags de baixa frequência: Utilizadas em aplicações de curto alcance, como sistemas de controle de acesso e
identificação de animais. - Tags de alta frequência: Oferecem maior alcance e capacidade de armazenamento, sendo utilizadas em aplicações
como gestão de estoque e rastreamento de ativos. - Tags de ultra alta frequência: Possuem maior alcance e velocidade de leitura, sendo ideais para aplicações que exigem
alta performance, como logística e transporte.
O RFID é uma tecnologia versátil e poderosa que pode trazer inúmeros benefícios para as indústrias. Ao automatizar
processos, aumentar a precisão e oferecer maior visibilidade, o RFID contribui para a otimização da operação e a melhoria
da competitividade das empresas.